- Cooling capacity range : 140 kW to 875 kW
- Fluid : Soft Water / water + glycol solution
- Refrigerant : R134a
- Operating ambient temperature range : +10 to + 50C
- Best fluid outlet temperature : 15degc, At ambient : 35degc & ∆T : 5 Deg C
- Condenser Type : Water - Cooled, Fin & Tube
- Evaporator Type : Brazed Plate / Shell & Tube Heat Exchanger
- Operating environment : Indoor / Out door - Shelter from rain, dust, insects, humidity, sunlight
- Power supply : 1 PH / 3 PH, 220V / 415 V, AC, 50/60 HZ
- MOC of wetted parts : SS 202 / 304 / 316 / CU
- Fluid loop : Open loop
- Noise level : < 85 db
- Life expectancy : 10-15 years
Screw Chiller
Werner Finley’s Screw chillers are distributed under two series, broadly categorised based on cooling media i.e. Air-Cooled or Water – Cooled, the water quality used for the process and the ambient temperatures under which they are made to operate. All these chillers are made to be compatible for both indoor and outdoor installation. Screw chillers are available starting from 40TR and above. Werner Finley offers a bare chiller option wherein the water reservoir and pump are absent. In a package chiller there can be 2 skids; one for the chiller and one for the tank and pump. This option is customised based on the client’s availability of space.
Screw chillers contain single or two compressor circuit redundancy options depending on the capacity. Screw chillers are designed to work for varying load. Two types of compressor systems are available based on the nature of loads i.e STEP CONTROLL & STEPLESS CONTROLL. STEP CONTROLL Compressors work for step loads i.e 25%, 50%, 75% & 100%, whereas STEPLESS CONTROLL Compressors work for infinite loads i.e anywhere in-between 25% to 100%. Each chiller comes with a dedicated microprocessor or PLC-based chiller controllers which determine the number of compressors to run based on the amount of heat load. Due to these features, the Air Cooled Screw Chillers are energy efficient and offer redundancy based on the criticality of the application.
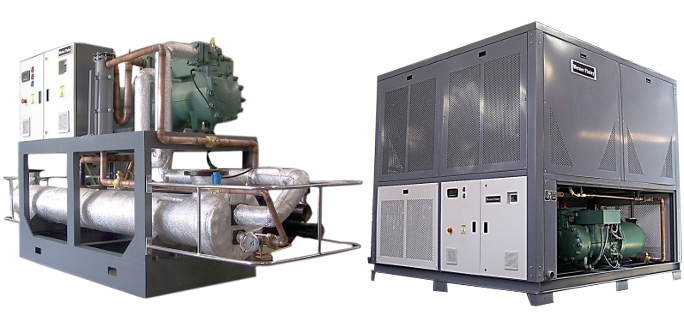
Our Applications
Solar and Wind Energy, Health Care, Data Center, Power Electronics, Machine Tool, Induction Heating, Welding, Hydraulic Oil Cooling, Paint Manufacture, Pharma, Chemical, X-Ray Spectrometer, Vacuum Systems, Breweries, Food Processing, Plastic, Concrete Batching